The Air Save project is a groundbreaking initiative designed to optimize compressed air systems in manufacturing by focusing on air distribution networks and end actuators. In a typical manufacturing setup, countless machines and workstations rely on such systems, creating a complex network of end-uses that require efficient management to reduce waste and costs.
To address this, Air Save employs an Industrial Internet of Things (IIoT) system that automates real-time monitoring of environmental and financial metrics. Data, including pressure, flow rate, and system cycle times, is continuously collected and analyzed by intelligent systems. With thousands of data points generated every minute, manual analysis becomes impractical, making Machine Learning (ML) crucial for identifying leaks and other anomalies.
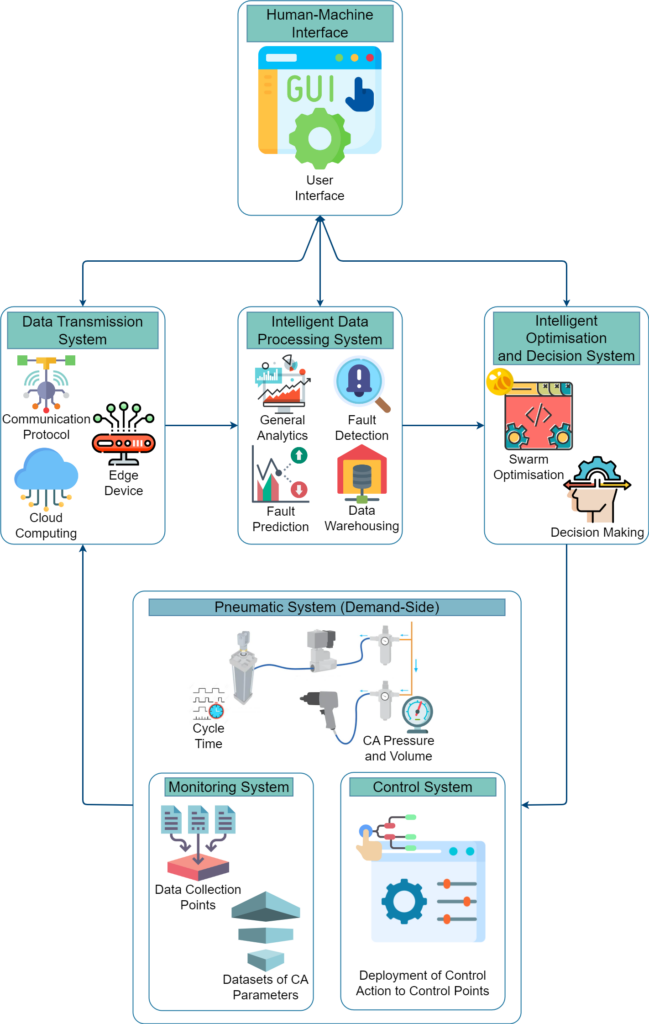
The project integrates ML algorithms to identify and classify leaks by analyzing complex data relationships. Using statistical processing, this data is fed into AI models that detect faults and categorize system statuses. Beyond fault detection, Air Save uses swarm intelligence algorithms to control system behavior proactively, even in fault conditions, ensuring manufacturing productivity remains consistent. Full automation of these controls is feasible with the right equipment, allowing immediate responses to detected faults.
The system also reduces reliance on traditional fault-finding methods like ultrasonic tools, offering a more efficient, sustainable approach. By deploying Air Save in real manufacturing environments, the project aims to enhance both maintenance practices and sustainability in the industry.
This innovation is currently patent pending with the UK Intellectual Property Office, marking a step forward in automated and intelligent air management solutions for manufacturing.